Oil tank sludge, an amalgamation of oil residues, sediments, and contaminants, presents a considerable challenge in the realm of petroleum storage and handling. Addressing this issue necessitates the implementation of sophisticated oil tank sludge treatment methods aimed at efficient removal and remediation.
Understanding Oil Tank Sludge Composition
Oil tank sludge is a complex mixture comprising hydrocarbons, water, solid particulates, and microbial growth. This amalgam often forms due to the settling of suspended solids, oxidation of hydrocarbons, and microbial activity, culminating in a viscous, challenging-to-handle substance. The thermal desorption unit can dispose of oil sludge in an eco-friendly way.
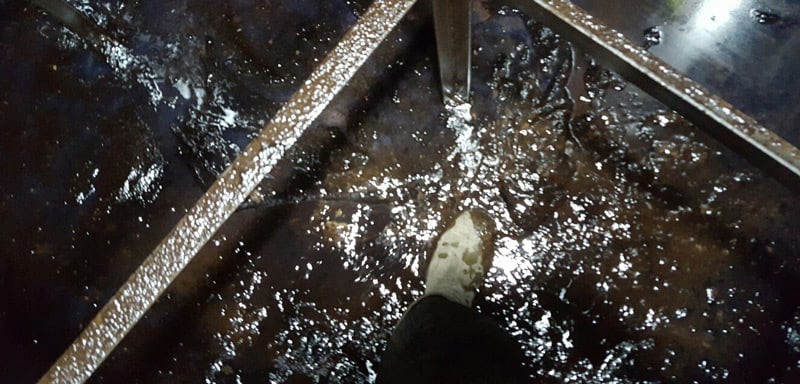
Mechanical Methods: Sludge Removal Techniques
Mechanical approaches constitute initial steps in oil tank sludge treatment. Utilizing specialized equipment such as sludge pumps, skimmers, and centrifuges, these methods focus on physically extracting sludge from the tank bottom, separating the heavier sludge from the liquid oil, and minimizing residual accumulation.
Chemical Treatments: Dispersants and Solvents
Chemical interventions play a pivotal role in breaking down oil tank sludge. Dispersants, surfactants, and solvents aid in emulsifying and dissolving sludge components, facilitating their separation from tank surfaces. This method enhances the efficacy of subsequent mechanical removal processes.
Thermal Treatment: High-Temperature Processing
Thermal techniques involving high-temperature treatments, such as incineration or thermal desorption, offer viable solutions for oil tank sludge treatment with oil sludge pyrolysis plant. These methods subject the sludge to elevated temperatures, vaporizing volatile components and converting hydrocarbons into recoverable forms.
Biological Remediation: Microbial Degradation
Innovative approaches incorporate biological agents for oil tank sludge treatment. Bioremediation employs specialized microbial cultures capable of breaking down hydrocarbons present in the sludge, aiding in the decomposition of organic components into less complex and environmentally benign substances.
Vacuum Distillation: Separating Oil from Sludge
Vacuum distillation stands out as a robust technique in oil tank sludge treatment. This method involves subjecting the sludge to reduced pressure and elevated temperatures, causing the oil fraction to vaporize and separate from solid residues, enabling the recovery of usable oil.
Ultrasonic and Chemical Washing: Surface Cleaning
Utilizing ultrasonic energy and chemical washes offers a targeted approach to oil tank sludge treatment by pyrolysis plant for sale. These methods dislodge adhered sludge from tank surfaces, enhancing the efficiency of subsequent treatments and preventing corrosion or blockages within the tank.
Dewatering and Solidification: Sludge Volume Reduction
An integral part of oil tank sludge treatment involves dewatering and solidification techniques. These methods reduce sludge volume by extracting water content and solidifying residual components, rendering the sludge more manageable for disposal or further processing.
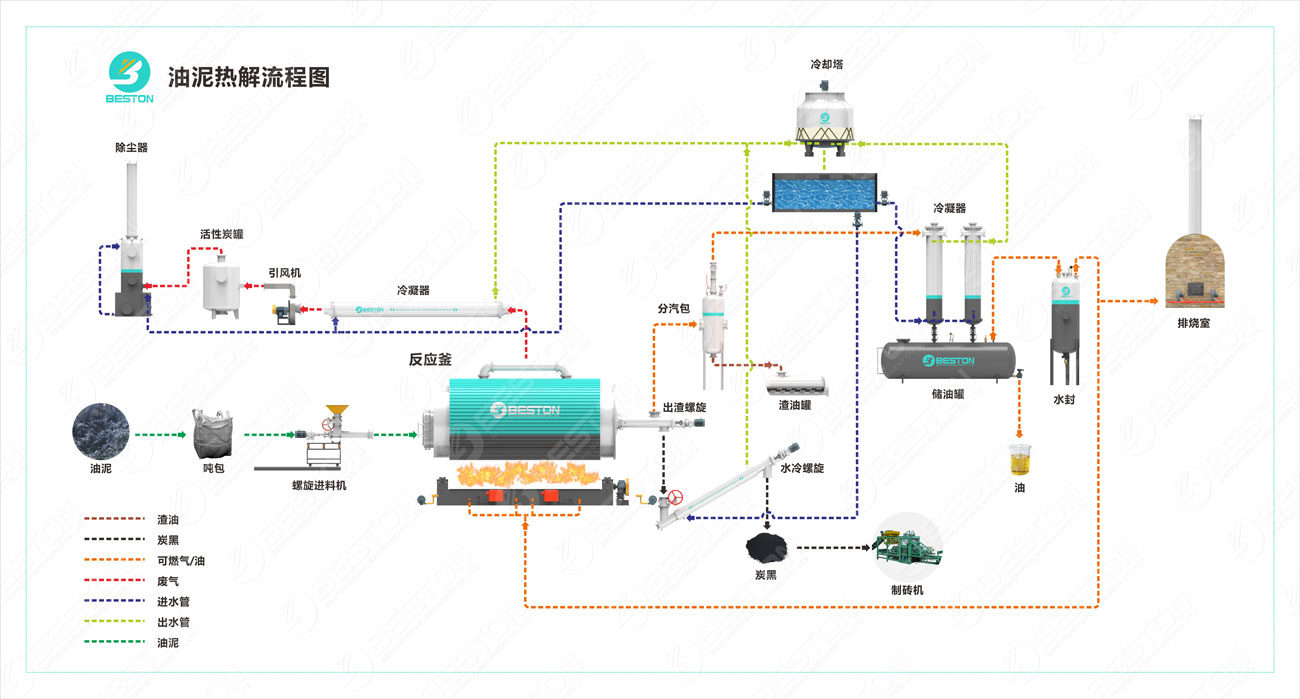
Environmental Considerations and Compliance
Throughout oil tank sludge treatment, stringent adherence to environmental regulations remains imperative. Efforts focus on minimizing emissions, proper handling of waste streams, and ensuring that treatment processes align with ecological standards and safety protocols.
Future Perspectives and Innovations
Continuous research and innovation in oil tank sludge treatment seek to refine existing methods and explore novel technologies. Advancements in nanotechnology, robotics, and bioremediation hold promise for more efficient, eco-friendly, and cost-effective sludge treatment solutions.
In summary, the confluence of mechanical, chemical, thermal, and biological methods constitutes the arsenal of oil tank sludge treatment. As technologies advance and best practices evolve, these methods stand as pillars in addressing the challenges posed by oil tank sludge, aiming for efficient remediation while ensuring environmental sustainability. More information on Beston Group here.